OIL & GAS INDUSTRY GAME-CHANGING TECHNOLOGY TRENDS
Current Climates Affecting the Industry
Increased oil and gas price volatility resulting from unpredictable geopolitical developments means producers have to cut costs to make sure they will be able to deliver attractive returns for investors. Although oil and gas prices have been increasing due to supply constraints, the possible economic disruptions from war, sanctions and the pandemic have introduced new risks to oil & gas producers. These risks can be mitigated through reductions in their operating costs, enhanced efficiency and by improving the quality of the oil and gas produced. The aim is also to increase productivity while improving worker safety and making production transparent for environmental compliance.
The Need for Change
For the past few decades, oil & gas company operations have been limited by proprietary automation and control systems. These closed networks of upstream and midstream systems are expensive to maintain and difficult to implement. They are not future-proof, inflexible and difficult to upgrade or adapt to support a variety of applications without investing a great deal more money. Having closed, proprietary systems with low interoperability and working with rigid structures while at the mercy of the legacy wellhead system vendors has created a greater need for rapid change for the players in the industry.
Considerations for Better Wellhead Systems
Features and functionality required for improved wellhead control systems include the following:
• Standardized hardware incorporating all communication, monitoring and control functions
• High-security monitoring and control for all types of upstream and midstream production
• Open architecture software that runs on standard hardware
Technology IS the Answer
In the ever-changing world of industrial computer technologies, wellhead and other upstream and midstream operational systems can benefit from periodically adopting a more advanced and better automation technology. For example, edge controllers have come a long way and are increasingly more intelligent. Some offer high computing power – with rich interfaces and cloud connection for seamless transfer of data. Some are ruggedized and offer C1D2 certification for reliable operations in explosive environments. Some support open-sourced OS such as Red Hat Enterprise Linux (RHEL) for its security and cloud deployment focuses. These controllers can meet industry requirements, checking all the boxes for effective operation.
By embracing new technologies, oil and gas operators can solve their long-term challenges and achieve higher efficiency and reliability. In addition, they can enhance their bottom line with higher productivity and by reducing their operating and maintenance costs. These technologies also allow for better security and analytical insights beyond what the legacy systems could provide, especially in a time of rising cybersecurity threats. New IIoT technology is the answer to the past, present and expected future challenges for the industry.
Emerging Industrial IoT Solutions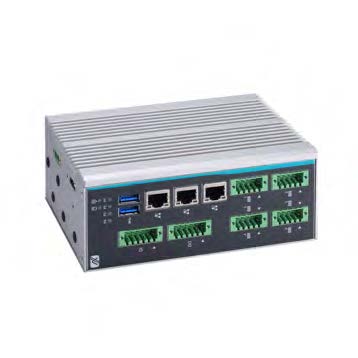
By introducing a standard, off-the-shelf advanced controller technology and analytical software capability at the edge, and creating a universal standard for these controllers, oil and gas operators can now easily take advantage of newer technologies to enhance their upstream and midstream processes and respond faster to challenges in the field. Having a universal, open-architecture platform that is flexible to expand and easy to upgrade – with built-in security, scalability, high interoperability with validated middleware and edge analytical software, remote control capability and more – is a game changer for the industry.
A Universal Wellpad Controller (UWC) Project*
Developed by leading technology providers such as Intel®, in conjunction with prominent, open-source enterprise software companies and major oil & gas corporations, a universal wellpad controller project emerged as the solution for the industry’s age-old challenges. By using standard off-the-shelf hardware such as Axiomtek's C1D2 certified ICO300-83M DIN-Rail controller, together with open architecture OS and edge analytical software, the industry now has a unique solution that solves its long-term problems.
Axiomtek wellpad controllers are designed to offer ultra-low power consumption for use in the field where solar energy is the main source of power. Wellpad operation modules and analytical software can be easily ‘dropped’ into the standardized controller for a quick setup and to provide operators with control and monitoring functions throughout all aspects of the well production cycle. It is also designed to work well as a controller for a variety of upstream and midstream activities.
The advantages of using a universal wellpad controller include the following:
• Reduced costs from equipment standardization with pre-validated and pre-integrated controller and software
• Fast and standardized deployment
• High flexibility with no vendor lock-in
• Innovation in software modules without changing the hardware
• Near real-time analytics at the site
• Easy upgrade, testing and deployment of new features/functionality/software
Axiomtek Universal Wellpad Controller and Edge Industrial Computer
Axiomtek has been a leading global provider of industrial IoT systems for the energy industry for over 30 years. Axiomtek ICO300-83M and eBOX710-521-FL fanless embedded systems are good examples of solutions that are purpose-built to serve oil and gas operations. Developed for the Universal Wellpad Controller (UWC) project, the ICO300-83M features include the following:
• Intel Atom® x5-E3930 Processor (E3940 coming soon)
• C1D2/ATEX certified
• Rugged, with wide Operating Temperature Range of -40°C to +85°C
• Supports TPM 2.0 for better security
• Ultra-Low Power Consumption
• Rich interfaces with 6 isolated COM, isolated DIO (8-in/8-out), and 3 GbE LAN
• 9 to 36 VDC wide voltage input with OVP, UVP, OCP, RPP
• Supports Cold Boot at -40°C
The eBOX710-521-FLis a workstation-grade embedded system that offers complete expandability and full-featured I/O interfaces. It is designed for oil & gas off-field operations and supports machine learning, deep learning, edge computing and other AIoT applications. Its features include the following:
• Scalable Intel® Xeon®, 9th/8th gen Intel® Core™ i7/i5/i3 or Celeron® processor
• Supports 2 DDR4 ECC/non-ECC memory, up to 64GB
• Dual swappable 2.5" SATA HDD drive bays with RAID 0 &1
• Supports triple independent display with DVI-I, HDMI, and DisplayPort interfaces
• Rich interfaces with 6 GbE LAN, 6 USB 3.2, and 1 PCIe x4 slot
• Rugged, with wide Operating Temperature Range of -40°C to +70°C and vibration endurance up to 3G
• Supports flexible I/O window
*Source Intel Universal Wellpad Control
https://www.intel.com/content/www/us/en/energy/intelligent-wellpad-control.html